In 2022, Krones gave itself a new mantra, “Solutions beyond tomorrow”, and implemented a new vision. The company explains what that vision includes and what it means for customers.
Humankind is facing major challenges that do not stop at the beverage and food industry, including the ever increasing pace of climate change and the growing world population.
To solve these challenges, humanity is facing a great feat of strength that it can only accomplish together.
Krones incorporated sustainability into its product development process more than a decade ago.
The foundation was laid back in 2008, with the enviro management system certified by TÜV Süd.
Sustainability is becoming the biggest innovation driver in new and future developments. While digitalisation and fully comprehensive services in production will also play a decisive role in increasing performance and reducing resource consumption.
Krones is seeking to apply sustainability attributes even more comprehensively to its entire portfolio in process technology, filling and packaging technology, and intralogistics.
The company defines this ambition in its new corporate vision, focusing on three challenges facing humanity – climate change, feeding the world’s population, and the responsible use of packaging materials. Krones’ ambition is to contribute to solving these three pressing issues.
This is also reflected in the new Krones claim: Solutions beyond tomorrow.
But how can beverage bottlers meet the challenges?
Beverage industry: on a good path
Beverage bottlers are in a more comfortable situation than some other industries.
There are already many solutions available that reduce CO2 emissions or contribute to the use of renewable energies.
One example is the biomass conversion Phoenix BMC by Steinecker, which allows brewing residues to be used energetically and fermented into biogas.
The residues are first converted into valuable raw materials. After the valuable ingredients have been extracted from brewer’s grains, yeast and malt dust, the remaining mass can be converted in a biogas plant.
Phoenix BMC is part of another major innovation of recent years: the energy-autonomous and CO2-neutral brewery Brewnomic.
World population continues to rise
Ensuring food security for the world’s population is another component of Krones’ vision.
At the end of 2021, there were already 7.9 billion people living on earth. According to the United Nations, the forecast for 2050 is around 9.74 billion.
Supplying people with packaged water must be guaranteed in the same way it is with food.
This is where one of PET’s advantages comes into play – the material is unbreakable.
In regions where transport routes are not well developed and access to clean drinking water is very limited, PET bottles are easier to transport.
PET bottles also have a much lower environmental impact than other materials when transported over long distances.
Since water is mainly bottled in PET bottles, this type of container will continue toplay a major role in the future, particularly as beverage companies work to meet the increasing demand. According to Global Data, growth rates will average 3.7 per cent annually until 2024, so bottling plants need machines that have greater capacity.
In response to this, Krones developed the world’s first wet-end block, achieving an output of 100,000 0.5-litre water bottles per hour.
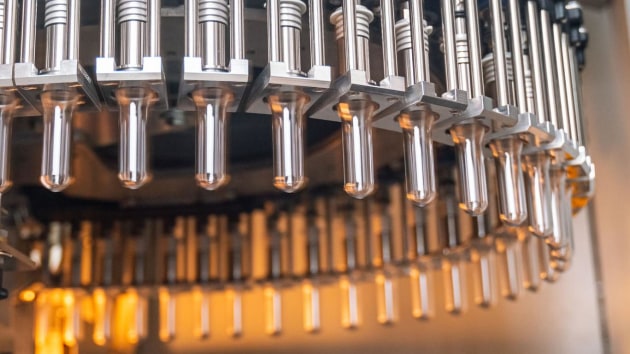
The basic production sequence is just the same as in a conventional ErgoBloc L. But the individual machines have some key differences.
The filler posed the biggest challenge for the development team, because there are physical limits to the standard approach of “bigger carousel equals higher output”.
At some point, the masses to be moved, and the forces acting on them, simply get too big to reliably maintain a stable process. Even though these forces might not be sufficient to set the filler itself shaking, they would certainly cause the product to slop over.
To prevent this, the block features two modularised filling units and two modularised cappers, which are still constituent parts of a single integrated block with just one valve rack and one sorting system for closures.
When compared to a 72,000-bph block built in 2015, more than 16 per cent in energy savings were achieved. As a result, the TCO is up and Scope-2 emissions are down.
Sustainability and PET – a contradiction?
In 2021, there was more than 533 billion PET bottles produced for alcoholic, non-alcoholic, and dairy beverages. That is expected to exceed 600 billion by 2025.
What is often forgotten is that PET can be sustainable if the materials are produced in a resource-conserving manner and kept in a closed cycle.
Companies like Krones already offer options, starting with material-saving container design, through low-energy container production, and right up to the recycling of used plastics with, for example, the MetaPure recycling systems for PET and polyolefins.
Other ways to reduce CO2 emissions includes light weighting PET bottles. A Krones customer saved about four per cent in bottle weight, entirely without reducing production performance. It also cut costs due to using less materials and saved the customer 720 tonnes of CO2 annually.
Furthermore, the use of rPET still offers the biggest opportunity to save CO2.
If 100 per cent recyclate is used on the 100,000-bph ErgoBloc, up to 3,600 tonnes of CO2 per year can be saved.
Secondary packaging also offers opportunities to make material savings and reduce emissions. For example, LitePac Top – sustainable cardboard clips for cans and disposable PET bottles – are made of renewable raw materials and are 100 per cent recyclable. Despite the minimalist use of materials, the container is stable, comfortable to carry, and convenient to remove.
There there is no “one solution for everything”. Many individual components create the big picture.
Potential savings on the way to sustainable production must always be considered on a customer-specific basis.
Every small adjustment screw that is turned contributes to the bottom line.
This story first appeared in the April/May edition of Food & Drink Business magazine.