Global systems supplier, GEA Group, has launched its new Direct Sprayer DS 25, a solution for industrial tank cleaning in the food and beverage industry, specifically designed for tanks with rotating installations.
Strict hygiene standards, contamination prevention, and resource efficiency are key challenges in food and beverage production. However, cleaning tanks with internal installations poses a particular challenge: the undersides of agitator blades often remain in the spray shadow and are not adequately cleaned by conventional methods. The most common solution has been to completely flood the tank with cleaning liquid – a resource-intensive and time-consuming process.
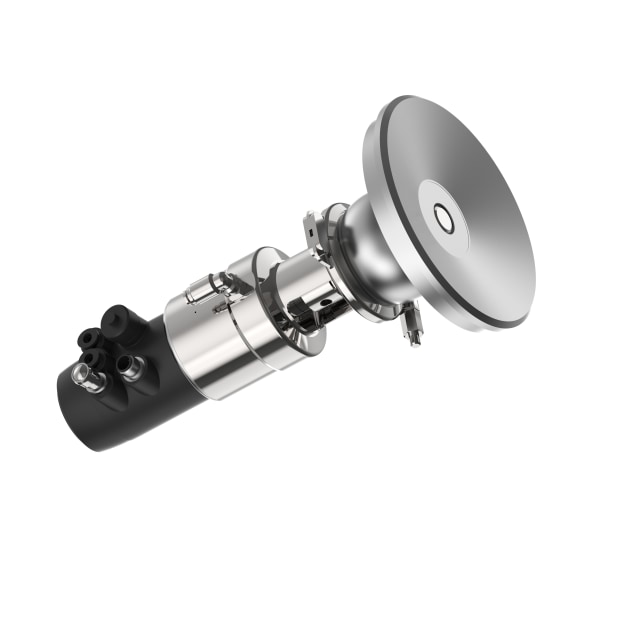
GEA’s Direct Sprayer DS 25 uses patented spray technology to remove residue from the undersides of agitators, pipes, and flow breakers, without impacting the system mechanics. The cleaner is flush-mounted into the tank wall and can be positioned flexibly, ensuring full coverage inside the tank. The patented valve disc only opens when activated, ensuring an even distribution of the cleaning fluid.
A case study from yoghurt production used this method to cut water use by 84.5 per cent and shorten cleaning time by 87.5 per cent, compared to traditional tank flooding.
With a spray force of up to five kilograms, the GEA Direct Sprayer DS 25 can effectively remove tough residues. Conventional cleaning systems often operate at lower forces, requiring longer exposure times or additional chemicals.
The full-cone spray of the DS 25 cleans more efficiently while reducing resource consumption. With a cleaning range of up to five meters, the full-cone spray is also suitable for large tanks and reaches areas that previous solutions often left uncleaned.
GEA product sales manager for cleaning technology, Jana Zimpel, said unlike alternative retractable cleaners, which often have a hollow cone or operate with a fan spray, our spray pattern is a true full cone.
“This time saving can be directly used for additional production capacity. In yogurt production, for example, this means more batches per day or faster recipe changes without compromising efficiency,” said Zimpel.
The GEA Direct Sprayer DS 25 has been developed for use in the beverage, food, dairy, pharmaceutical, and home and personal care industries. It is advantageous in production environments with frequent recipe changes, strict hygiene standards, and demanding cleaning requirements. The system delivers fast, efficient cleaning while minimising water use and keeping production running smoothly, and can be easily integrated into existing systems.