Australia has long been recognised for its culinary diversity and wide variety of food and beverage products available directly to the consumer. According to Innova Market Insights, in the well-established Australian market, consumers are seeking product diversification and novelty, especially in everyday staples, snacks and sweet treats, driving increased uptake in these categories.
Australia’s multicultural demographics, and wide range of available cuisines further extend the need to stock greater variety of ingredients, food, and beverages.
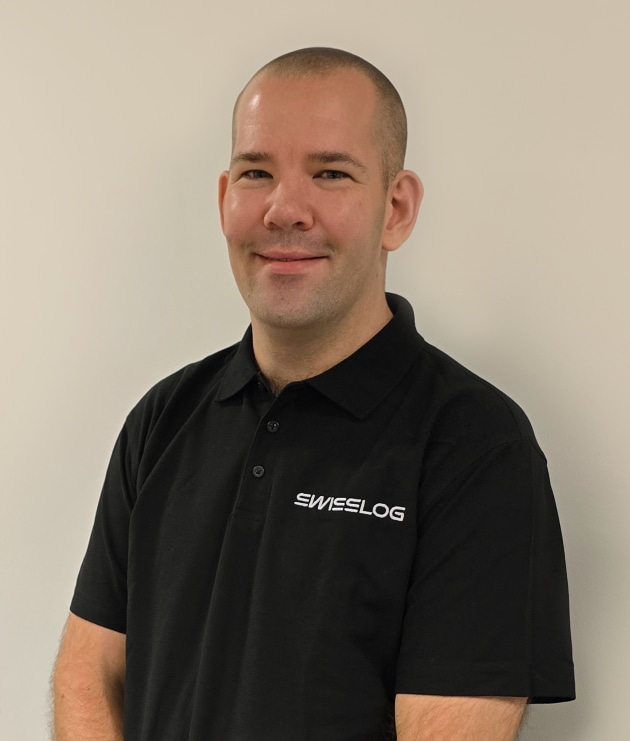
Source: Swisslog
Stocking such a wide variety requires intelligent systems behind the scenes, to enable food and beverage manufacturers to maintain efficiency and productivity.
“To remain competitive, it’s imperative that food and beverage manufacturers make optimum use of their warehouse space, are able to get product in and out faster, and can keep levels of freshness and quality high,” says Swisslog Food and Beverage sales consultant, Joseph Kutek. Swisslog has automation systems across the globe that have been in continuous operation for more than 30 years at multiple food and beverage manufacturing sites.
“Consumers want freshness and product variation, and manufacturers want to be both time- and cost-effective, whilst minimising waste and their environmental footprint. These are areas where an intelligent and fit-for-purpose warehouse automation solution can make a significant difference,” says Kutek.
Space optimisation – utilising height
With industrial land selling at a premium, and prices rising, optimising utilisation within an existing warehouse space is one of the best ways to increase product diversity.
“For optimum space utilisation, food and beverage manufacturers can use automation to create solutions with greater density, or greater height – sometimes both – to be able to store more SKUs within the same footprint,” says Kutek.
“In Sydney and Melbourne in particular, there’s a lack of supply of available warehouse space currently, so manufacturers are looking to get more out of their existing sites,” he said.
For warehouses with lots of vertical space, Swisslog’s Vectura high bay warehouse pallet stacker cranes can operate at heights up to 50 metres. They can handle large and unusual loads, in single, double, triple, or multi-deep layouts – and they perform equally well in frozen food warehouses down to -30°C as they do in ambient environments up to +50°C.
“Vectura cranes also have a unique mast design that enables a lower weight, which results in around a 20 per cent lower energy consumption compared to other pallet cranes,” adds Kutek.
To further advance the sustainability credentials of Vectura cranes, Swisslog’s latest designs can capture energy generated from the vertical axis downward motion of the crane’s carriage and redirect this energy to offset the energy draw from the horizontal motion of the crane and vice versa. This regenerative energy capability reduces total energy draw by up to 20 per cent.
Space optimisation – utilising density
For warehouses that don’t have height available, maximising the density of the automation solution is one of the best ways to increase product range.
Swisslog’s PowerStore pallet shuttle system enables storage of up to 60 per cent more pallets compared to manual systems, and can be customised to suit all shapes and sizes of building. Like Vectura cranes, PowerStore can comfortable and reliably operate in temperatures from -30°C to +50°C.
“PowerStore also enables throughput of up to 400 pallets per cell per hour, making it ideal where high performance and high density are both required,” says Kutek.
“Swisslog has also refined PowerStore over the years, and its smart positioning system, combined with a unique design of rack interfaces and deflection of pallets, all contribute to error minimisation and high system availability,” he adds.
Both Vectura cranes and PowerStore shuttles are examples of Automated Storage and Retrieval Systems (ASRS), an area in which Swisslog has extensive expertise, and can customise solutions to boost warehouse quality, flexibility, and efficiency.
Traceability
A major benefit of using warehouse automation and software is the added level of product traceability throughout the supply chain.
“Increasingly, both consumers and regulators are looking for full farm-to-fork traceability, to highlight quality as well as transparency of origins,” says Kutek.
“For example, Swisslog’s SynQ software can provide useful data on the system, which can be used both for traceability purposes, and also to look for process optimisation and further efficiencies,” he adds.
SynQ is a proprietary software developed by Swisslog that stands for synchronised intelligence. It synchronises people, process, and machines for efficient operations. In addition to being a Warehouse Management System (WMS), it can perform the task of a WCS (Warehouse Control System), or MFS (Material Flow System), and can seamlessly interact with ERP (Enterprise Resource Planning) and e-shop systems.
“As an intralogistics organisation, we cover all items within the warehouse automation system and can make sure they are fully traceable, including batch numbers, expiration dates, and visibility on storage down to individual products.”
Freshness
To keep product quality high and food fresh, it’s important for food and beverages to stay within the correct temperature ranges.
“This is an area where automation can shine. Warehouse automation technology, coupled with our intelligent SynQ software, can create environments where food and beverages are stored in optimum temperatures for the right periods of time, delivering greater product quality, and minimising waste from spoiled products,” says Kutek.
Local and global experience
Swisslog has implemented warehouse automation solutions for food and beverage organisations locally and globally, including:
- A new Victorian warehouse for a major snack food manufacturer, involving Vectura high bay warehouse stacker cranes, and a capacity to handle 56,000 pallets initially with room to expand to 75,000 in the future as the business grows.
- BevChain, a leading beverage giant and wholly owned subsidiary of Linfox, which increased storage utilisation by around 60 per cent in their existing facility. BevChain installed PowerStore in their existing 24/6 facility in NSW, which includes over 30,000 pallet locations over five levels.
- Treasury Wine Estates in South Australia, which added Swisslog’s advanced SynQ software to complement a Swisslog automated storage and retrieval system (ASRS) that has been installed since 2005 and has enabled a wide variety of bottle, label, and carton variation to be handled at high speeds with accurate delivery fulfillment.
- HelloFresh prepared meal delivery service, where Swisslog installed an AutoStore grid-based automation system for their warehouse in Texas, USA. By leveraging AutoStore and SynQ, HelloFresh enhanced operational efficiency and scalability in their distribution centre, achieving higher throughput, accuracy, and flexibility while accommodating a growing menu and customer demand.
Food and beverage automation in 2025 and beyond
“As we look at 2025 and beyond, it’s clear that increasing product variety is not going away in the food and beverage industry. We’re currently seeing growth in alternative proteins, alternative milks, non-alcoholic beverages, meal preparation solutions, and functional health products – particularly beverages that go beyond just quenching thirst,” says Kutek.
“These are expected to continue strong performances in 2025, and in the future new trends will arrive that companies will look to quickly adapt and capitalise on. Having flexible, adaptable, and efficient warehouse automation will allow food and beverage manufacturers to pivot to new products, meet growing demand, and improve their performance.”