From two friends with an idea to a global company with 800 employees, materials handling company Combilift recently celebrated its 25th anniversary, and is showing no signs of slowing down. Kim Berry visited Combilift HQ at Monaghan, Ireland, courtesy of the company, to see the business firsthand.
Martin McVicar and Robert Moffett started Combilift after mutual success at Moffett’s company, Moffett Engineering. Moffett had designed and manufactured the first truck-mounted forklift, the “Moffett Mounty”, which revolutionised the materials handling industry.
Not to be outdone, McVicar, who had left school at 17 but was studying engineering modules through Open University while working, had joined the company for work experience to become the company’s chief engineer before he even turned 20.
Food & Drink Business sat down with McVicar and other members of the team at Combilift HQ in Monaghan, Ireland, over the course of three days during the company’s 25th birthday celebrations.
McVicar said he never had any doubt about the business succeeding.
“One of the things I remember from when we were setting up the company was about our ambition for the company.
“My ambition at that time was to grow the business as big, if not bigger, as Moffett, that was the benchmark. We are a much larger company than Moffett today,” he said.
Combilift entered the market with the C4000 model – the world’s first internal combustion (IC) engine, all-wheel drive, multidirectional forklift.
Combilift’s first employee – and still at the company – Mark White worked with McVicar and Moffett on the machine, initially in his lounge room.
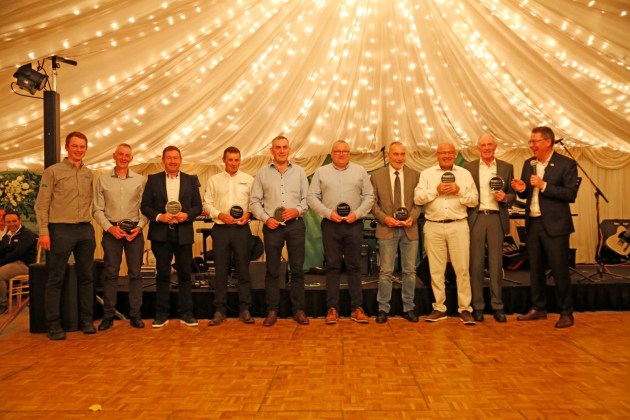
“Being able to load a product outside, then unload it inside offered excellent ROI for customers. We enhanced the multi-directional capabilities and established space and safety as core priorities right back then, as they still are today,” White said.
When asked about highlights from his 25 years at Combilift, White, said seeing the company grow from the original three to 700 at Monaghan and 100 around the world was one. The company’s can-do culture was another.
McVicar said that can-do attitude came from the very early employees’ approach to projects which then embedded into the foundation of the company.
It took the company 350 employees before it set up a HR department.
“The HR function is more into facts and figures, rules and regulations, what’s possible, and what’s not, rather than giving people the freedom to be as more creative.
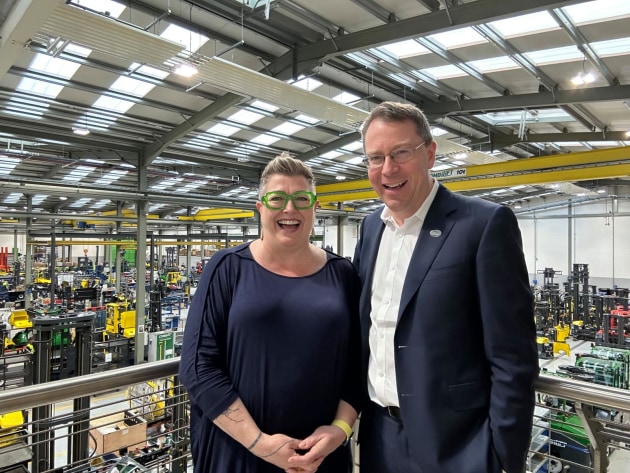
The challenge is keeping that creativity without becoming too systematic as we grow our staff more and more and overseas,” McVicar said.
White said the company still embodies continual development.
“We are always developing new machines, new ways of doing something, or finding solutions. We listen to our customers and salespeople, so we know what’s needed in the market.
“Engineers can make anything, but if there’s no market for it, then there’s no value in it.
“We have to secure our market to ensure our designs have value. We also protect all our designs with patents and design copyrights, which give us a leading edge over our competitors,” he said.
The company currently has around 140 patents worldwide.
Continual growth
In 2011, Enterprise Ireland offered McVicar a place in a Leadership for Growth program with Stanford University.
“I took a lot from the course, mainly watching our US customers and US culture. They think big and they’re not afraid to promote their success.
“I feel one limitation of Irish companies is we don’t preach enough about how good our businesses are. And of course, if you don't get your name out there, how can you expect to grow? So, setting a vision for the business became more ambitious; we could grow the business to a billion-dollar company.
“Before completing Leadership for Growth, I was very much a spreadsheet person thinking that if we grew 10 per cent a year we’ll eventually get there. I was calculating that from our 70-million-euro turnover at the time.
“Then I thought, what if we went to 15 per cent? Then we double the business every five years. It was a simpler message for people to understand and now that’s how we approach every area of the business.”
Today, Combilift’s top five markets are the US, UK, Germany, France, and Australia. It makes around 10,000 machines a year, all built to the specific requirements of the customer, and in March celebrated the production of its 75,000th truck.
Local presence
McVicar acknowledged that when it comes to the food and beverage sector, Combilift has a closer relationship to the third-party logistics (3PL) companies distributing the products than the manufacturers themselves.
“But we’ve noticed a model developing in the UK and across Europe where the 3PLs are building premises beside the food and beverage manufacturing plants,” he said.
Littlewood agreed, saying similar structures were happening in Australia.
You can see this happening, for example, Arnott’s automated distribution centre at its Huntingwood plant in Sydney’s western suburbs.
“There is a lot of potential for Combilift in the food industry in Australia, we’re already working with some of the global companies like Unilever,” he said.
One industry the company is doing a lot of work in is pet food.
“We’re seeing rapid growth in that market segment because the product is heavy, the manufacturers need to store volume and they need selectivity for shelf life. The Aisle Master adds tremendous value for these companies,” McVicar said.
In Australia, more than two-thirds of Australian households own at least one pet and they spent $17 billion on pet food in 2022.
Combilift has also made inroads with packaging companies through existing and established connections with operations in other countries.
Sustainability
Combilift reinvests seven per cent of its revenue into R&D. McVicar said for the last five years, around 98 per cent of that investment has gone into electric powered equipment.
He said that for the company, nearly all the vehicles it brings to market are electric powered, but the sustainability aspect goes beyond just the machine.
“We are very focused on making our vehicles more environmentally friendly. We’ve worked out ways of measuring the efficiency of the electric power as well. But it moves beyond that to asking how we can enable our customers to make their warehouse utilisation more environmentally friendly.”
The company does that from the first phone call, with Combilift providing free warehouse design to new customers.
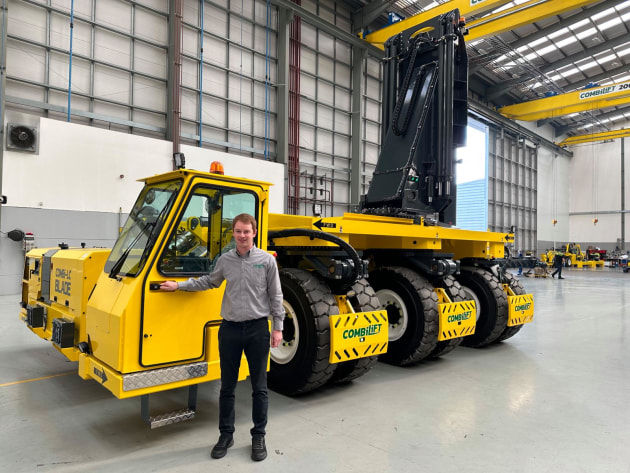
“We’re bringing tremendous value to a company with that service because it shows them how they can make their business more sustainable,” he said.
The anniversary also provided the ideal opportunity to announce its latest initiative – its own entry into the renewable energy sector with the Combi-LC.
Developed over the last five years, the unit is designed transport wind turbine components that are up to 115 metres long and weighing up to 70 tonnes.
Siemens needed a novel method to transport the finished blades from the manufacturing facility to the dispatch area. The companies have worked closely together with a handful of versions before launching the Combi-LC.
The root side unit features a cab, at the request of Siemens, which is understandable when you consider it is five kilometres from factory to warehouse. When it’s not carrying a load, the machine – powered by a 75-tonne capacity diesel engine and equipped with 12 wheels – can travel at 10km/h, saving the operator time on the commute back to the factory. The 12 wheels offer versatile multidirectional steering with six wheels.
Combilift designed a first-of-its-kind attachment that grips the massive cylindrical end of the blade and firmly affixes to the generator hub. Its ’tip side’ carrier unit smoothly manoeuvres beneath the blade, supporting it by a hydraulic tilting table-mounted clamp near its narrower tip.
It has full remote-control operation and is fitted with ultrasonic sensors.
Siemens have ordered 20 for its offshore wind turbine requirements and McVicar and Littlewood see Australia as a major opportunity for Combilift to supply these units as its offshore wind industry develops.
In 2022, consultancy Wood Mackenzie forecast large-scale wind farms to increase tenfold from 34GW in 2020 to 330GW in 2030, that it would be spread across 24 countries (currently nine), and around $1 trillion would flow from the offshore wind industry over the next decade.
The federal Department of Climate Change, Energy, the Environment and Water declared an area in the Bass Strait off Gippsland as suitable for offshore wind energy in December 2022, and an area in the Pacific Ocean off the Hunter region in July this year.
An area of the Southern Ocean off Victoria and South Australia has been proposed, as has an area of the Pacific off the Illawarra region, with decisions yet to be announced.
The Bass Strait region off Northern Tasmania and the Indian Ocean region off Perth/Bunbury have been identified as priority areas for assessment.
Trucks keep moving
When asked about what he’d like his legacy to be, McVicar said first and foremost it was to continue to grow the business organically in Ireland and retain HQ and R&D in Monaghan.
“As our business continues to scale, we will probably end up setting up assembly plants in some other markets, but we will exhaust all possibilities here first.
“We haven’t saturated any industry or market, there’s room for growth with the major DIY stores but it is also smaller distributors and single store companies who don’t know about our products or the value they could bring to their business. There is still so much opportunity for us,” he said.
There were two things that were repeated to me by many people on many occasions, if Combilift maintains its innovation, creative, and customer-centric culture, the rest will fall into place.
This article first appeared in the October-November edition of Food & Drink Business magazine.