SMC Corporation Australia New Zealand recently introduced the next-generation AMS20/30/40/60 compressed air management system series to the market – designed to reduce CO2 emissions and cut energy consumption by up to 62 per cent.
Research shows that many plants are still privy to air leakage rates of between 20-50%, and this is where SMC’s energy saving mandate comes in.
Energy Saving Conservation Group.
Head of SMC’s Energy Saving Conservation Group, Bill Blyth said, “Not only are our customers focused on their bottom line, but they’re also concerned about their impact on the environment, and in many cases this may form part of their plan for Sustainable Development Goals (SDGs). We at SMC are dedicated to enhancing energy savings, to such an extent so that we have an in-house energy consumption team that works alongside customers to implement energy saving measures on the factory floor.”
Energy wastage at manufacturing and process plants is largely attributable to factors such as poor control of air consumption, undetected leaks and processes which are unoptimized for standby and shutdown times.
“The AMS series should form part of every customer’s energy saving journey and can be deployed to tackle these very issues,” Blyth said.
Bill highlights the three key benefits of the AMS as visualisation, CO2 emission reduction, and Scalability.
1) Problem-solving technology through visualisation
With its combination of regulator, wireless hub and residual pressure relief valve, the AMS is designed to monitor air consumption, pressure and the temperature in air lines – anywhere, everywhere and all at once.
The data collected forms the basis for defining preventative actions and maintenance tasks. “This is important as maintenance teams often find it difficult to collect specific air-line data, leading to insufficient maintenance actions and unexpected failures or energy consumption peaks,” Blyth said.
The AMS series is compatible with OPC UA, PROFINET, EtherNet/IP and EtherCAT.
2) Higher efficiency, less CO2
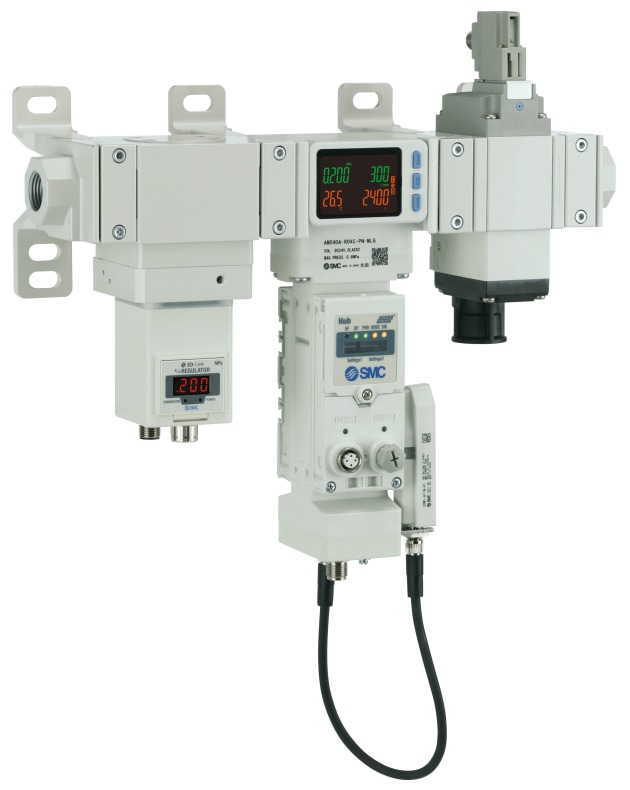
The AMS series’ secret to success lies in it’s intuititive standby mode feature. “Standby mode senses changes in the machine’s status – such as an air drop – and reduces the air pressure to reduce energy consumption,” Blyth explained.
Using programmable, automatic pressure reduction and shut-off times, the AMS series allows customers to reduce both compressed air and energy consumption, improving process efficiency and reducing CO2 emissions.
3) A scalable solution
“Along with improved maintenance capabilities, customers also benefit from a digitalised installation for higher levels of control. This capability leverages the advantages of innovative wireless technology, which is easy to integrate and avoids the need for communication cables.
“Wireless capabilities helps negate the need for electrically complex solutions.The AMS series promotes both time and cost savings through shorter installation and commissioning time, less wiring and fewer connectors,” said Blyth.
The decentralised system is compatible with OPC UA for direct data communications connection without the need of a PLC, as well as Ethernet I/P, Profinet, EtherCAT, and IO-Link devices. Using a single AMS20/30/40/60 hub, customers can connect up to 10 remote units with a maximum communication distance of 100 m radius.
“The AMS can be used across all industries and is complete with an IP rating of either 65 or 67, depending on the type of regulator deployed,” Blyth said.