A global food company was able to double distribution capacity at its existing site with an ROI of three years by working with Swisslog on a comprehensive automation solution.
The company provides high-quality products to customers around the world while also leveraging its distribution network to provide innovative solutions to others.
With demand for its processing services growing and seeing an opportunity to provide services to a leading food provider made the strategic decision to expand production and distribution capacity.
“We’ve seen food and beverage companies in Australia opting for similar solutions because labour shortages combined with increasing industrial real estate costs
mean it’s more productive to maximise throughput within your existing footprint with automation,” says Swisslog Australia and New Zealand Head of Sales, Sean Ledbury.
The challenge
The company had production and distribution facilities in an area that enables fast and cost-effective distribution to the region; however, the land required to physically expand the distribution centre (DC) wasn’t available and increasing capacities using manual processes would require tripling the workforce.
As a result, logistics specialists at the company began exploring the storage to expand the capacity of the existing DC. The automation would not only need to meet capacity and productivity requirements, but also be implemented in a way that didn’t disrupt customer service and could meet the company’s high food quality standards.
The company worked with a consultant to define their requirements for a complete, fast-turn automation solution that could receive products trucked in from the production facility across the street from the DC, provide high-bay storage, and automate layer picking.
Due to limited dock space, the solution would also need to support automated on-demand retrieval of completed pallets based on shipping schedules and loading requirements.
After a rigorous vendor and technology evaluation process, the company chose Swisslog based on the completeness of the Swisslog solution, the company’s food experience, and the strong fit between the two companies’ cultures.
The solution
Swisslog was the only vendor that studied the proposed solution and offered an alternate solution that met project objectives better than the original approach.
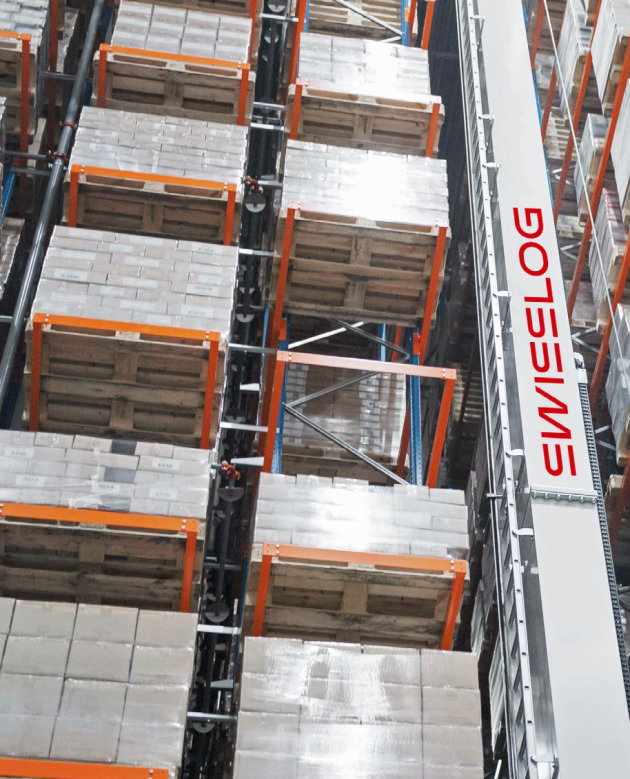
Rather than trucking products from the production facility to the DC as the company had planned, Swisslog proposed moving product using the Swisslog Monorail electrified pallet transportation system. This innovation eliminated the need for the company to develop and maintain a dedicated fleet of trucks and drivers to transport pallets the approximately half-mile distance between the production and distribution facilities.
Storage capacity at the site was increased through the deployment of an Automated Storage and Retrieval System (ASRS) consisting of two double-deep and four single-deep, energy-efficient Swisslog Vectura cranes.
The solution provides 18,000 pallet positions in 24,000 square feet of space. The ASRS is integrated with a robotic layer picking system to automate pallet building based on the requirements of the centre’s customers. Completed pallets are stored in the ASRS and retrieved as needed based on integration between Swisslog’s SynQ warehouse management software and the DC’s freight loading software.
This enabled a solution in which pallets could go directly from storage to trailer when it was time to load, which was essential because the company needed to maximise storage capacity within the limited footprint of the site and did not have space for pallets to sit on the dock waiting to be loaded.
SynQ controls all components of the solution as well as providing complete inventory management capabilities, including full inventory visibility from production through shipping. The software also makes it easy for the company to add SKUs as new relationships are developed with customers.
The deployment of the solution was completed on schedule and a Swisslog resident engineer helped ensure a smooth transition to automation by providing on-site training, establishing maintenance practices and auditing maintenance processes until company employees were prepared to assume responsibility for the solution.
From the software to the Monorail, ASRS and layer picking, everything works together as a single system that delivers the availability, speed, productivity, and visibility the company needed to maintain quality and support customers.
Food safety was a high priority throughout the solution development process. Each pallet is timestamped as it enters the Monorail and again when it is received at the DC and entered into the Swisslog SynQ warehouse and automation management system, so the company always knows where product is and how long it has been there. In addition,
the only time products have to be handled between production and shipping is for quality control. Finally, automation systems use food-safe lubricants and enable easy cleaning under and around the systems.
The results
Expanded capacity at lowest possible cost. By moving to high-density storage, DC capacity was doubled while keeping distribution close to production.
Fast return on investment. By automating transport between the two facilities and increasing process efficiency, the return on investment in the solution was just three years.
New revenue opportunities. The expanded capacity enabled by automation allowed the company to support the growth of its business.
Maintain quality and safety. The automation system improved inventory accuracy, reduced product handling and allowed the company to maintain the highest food safety standards.
Fast and reliable customer service. Automation supports the fast inventory turns required by short shelf-life products and has delivered high uptime over years of service.
System Overview
6 Vectura stacker cranes
- 2 double-deep storage
- 4 single-deep storage
- 18,000 pallet positions in 24,000 sq. ft. footprint
- Pallet conveyor system
Monorail pallet transportation from production to distribution
- More than 2,400 ft of track
- 10 Caddies
Robotic layer picking system
SynQ software
- Warehouse management
- Automation management, control, and visualisation
Resident engineer services