At Interpack this year, GEA presented new solutions for more sustainable manufacturing processes in the bakery industry. GEA says it is focusing on energy-saving production processes, new digitalisation tools as well as state-of-the-art technologies to ensure food quality.
Bake Depositor MO
The new GEA Bake Depositor MO volumetric cylinder depositor is ideal for depositing muffin, cake and cupcake mixes. It features the option of removing those parts that have contact with the food, allowing easy maintenance and cleaning. Removing the entire machine head is no longer necessary. Thanks to a special gasket designed for the wet part of the machine’s main structure, the novel stainless steel head uses specific solutions to avoid the accumulation of dirt and the proliferation of bacteria in the gaps between two metal parts lying on top of each other or positioned at a 90-degree angle.
Pneumatic consumption by the machine is practically eliminated thanks to a newly integrated system. The dosing piston is moved by a servo motor and the dosing cylinder can only be activated after a product has been inserted. With 12 dosing cylinders to control, the new system can reduce annual operating costs and significantly cut CO2 emissions. Guaranteeing high accuracy, the depositor has been designed to operate on continuous running conveyors or with tunnel ovens. Versatility is a key feature of the GEA Bake Depositor MO which is why the system is available with a fixed head, a vertical movement head or with both vertical and horizontal movement heads. Using brushless motors to drive the depositing head increases throughput, capacity and weight accuracy.
Retrofit Kit for ovens
The electric oven retrofit kit is a quick and easy way to switch from high-consumption gas ovens to more sustainable electric options. The changeover can be done swiftly and simply within a normal eight-hour work shift – depending on the oven characteristics. In addition, an electric tunnel oven consumes 15 to 20 per cent less energy than a gas-powered oven.
For customers wishing to switch to carbon-neutral production, the retrofit kit makes it possible to test manufacturing the baked product by way of electric baking before investing in a new oven. The GEA retrofit kit offers a great deal of flexibility in switching from gas to electricity or a mixture of both, depending on the product specification. Steam injection and turbo power facilitate fine-tuning of the baking process in an electric environment in order to achieve the desired baking result.
SmartControl for production lines
The new GEA SmartControl for bakery production lines incorporates all systems into one digital environment. In addition to the integrated control of production lines, the new visual interface lets operators view a large amount of information grouped together in a way that is both quick to grasp and manage. The most important functions are shown below.
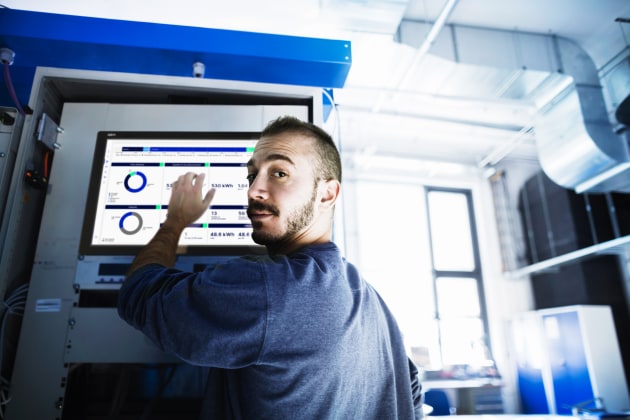
The machine documentation provides easy access to all necessary information regarding equipment and operation. This includes user manuals, operating instructions, maintenance schedules and more. The information is stored directly on the HMI (human-machine interface), making it easily accessible from the production line. This helps to ensure that all personnel are working with the most up-to-date information and eliminates the need for manual searches or paper documents. It streamlines processes, increases efficiency and reduces the risk of human error.
Users can keep track of any issues or malfunctions that occur within the equipment thanks to the alarm visualisation, history and statistics. The HMI displays real-time alarms and notifications, providing instant visibility of any problems. What is more, the system also stores a historical record of all alarms, allowing operating personnel to track trends and identify recurring issues. This feature includes statistical analysis tools that let users identify patterns and optimise processes. With this information at their fingertips, operators can quickly respond to any issues, minimise downtime and enhance overall equipment performance.
The “Machines Line Monitoring View” displays real-time data for each machine on the line – including third-party equipment – showing machine status, operating parameters and production statistics. Information is presented in an intuitive and easy-to-read format so that users can rapidly assess the performance of their equipment. This helps to improve production efficiency by providing real-time visibility of machine performance, allowing operators to quickly identify and resolve any issues.