Victorian craft brewery Burnley Brewing turned to automation to scale up operations and extend contract brewing arrangements with small brewers.
Burnley Brewing was nearing capacity at its brewery in Dandenong and experiencing strong growth.
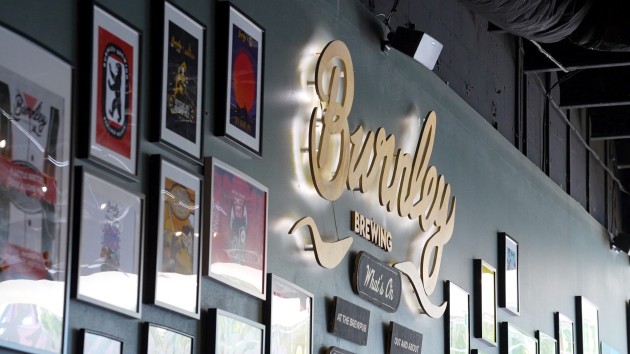
Head brewer Michael Stanzel said, “We wanted to take things to the next level by growing our own brand and expanding our contract brewing relationships.
“We approached electrical engineers, Bon Industry, and explained that we were looking to leverage automation to grow our operations and handle continuing demand surges. From day one, I could tell they were passionate about the project.”
Bon Industry recommended Rockwell Automation’s FactoryTalk Craft Brew, an industrial automation software developed specifically for the brewery industry.
The software starts at the edge where manufacturing happens and scales from on-premises to cloud to maximise operational efficiencies.
Mixing flexibility with scalability
Bon Industry electrical director, Gabriel Bonacci, said they wanted to give Burnley Brewing’s new Dandenong facility a smart manufacturing edge, greater choice, and greater ability to scale up operations in the future.
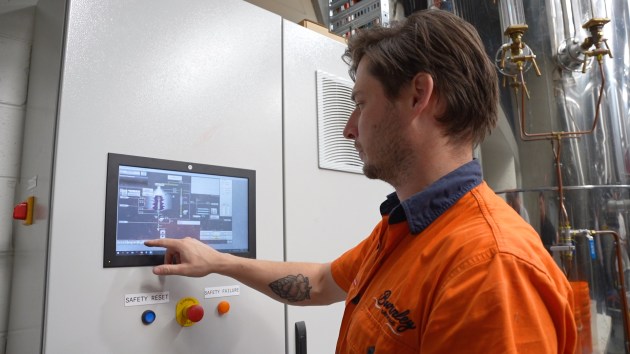
“Rockwell Automation’s FactoryTalk Craft Brew was the ideal platform for Burnley. The software connects easily to automation equipment of all types to seamlessly visualise automation performance and highlight critical areas for improvement,” said Bonacci.
With several Rockwell Automation programmable logic controllers (PLCs), drives, and industrial computers forming part of the new brewery, FactoryTalk connects them all together to create an integrated ecosystem.
FactoryTalk Craft Brew is designed as a modular software ecosystem where new modules can be added as required, allowing for flexibility and the option to upgrade operations as the business expands. The modularity also means the solution can be deployed quickly, with a standardised approach that reduces the need for operator training.
Stanzel said the project wasn’t without its difficulties.
“There were certainly some challenges along the way – like getting pressure differentials during the lauter process correct – but through collaboration between Rockwell Automation, Bon Industry and ourselves, we found the right solutions, and tested them to ensure they were working perfectly before commissioning,” he said.
The software is tested to top European and American Standards, and users can leverage Rockwell Automation’s global expertise for support and customisation. Additionally, Rockwell Automation can remotely access the hardware and software, and provide swift updates, monitoring, and repairs.
Rockwell Automation channel manager, Matthew Treeby, was delighted to be helping a local Australian-owned independent brewer.
“Rockwell Automation, together with our distributor NHP, has the support, resources, and availability to provide backup to companies of any size. When working on projects like Burnley’s new brewery, we can be dynamic and efficient, all whilst maintaining high levels of standards compliance and traceability,” Treeby said.
Automation simulation
During the concept stage, Bon Industry provided Burnley Brewing with a simulator to showcase how the new automated solutions could work for the new brewery.
“As soon as I tried the simulator, I noticed how user-friendly everything was. The programming was ultra-flexible, and it’s a major reason we chose Bonacci and Rockwell for this project. Since then, everything has surpassed expectations, from service, to product quality, to solution deliverables.
“Something I wasn’t expecting was adding automation to the milling and mashing processes. The automation makes the process almost too easy – now I need to find more things for my brewers to do,” Stanzel added.
Bonacci points out that the craft beer market in Australia is massive, thanks to a nation of ‘beer nerds’.
“Brewers often start with basic equipment to make beer. They are usually cheap investments which can be appealing, but with growth in scale, they become redundant.
“With something like FactoryTalk Craft Brew, you only need to invest once. This software does everything from cellar controls to full automation of the process grain silos and packing lines. The hardware is expandable, and everything syncs together so you never waste on an investment,” explained Bonacci.
“Also important to these craft brewers is traceability – being able to show their customers where the hops came from, where the beer was brewed, and all the finer details. With Rockwell’s software in place, the automation stores all the data, and brewers can use this when showcasing their story,” he said.
Data utilisation is one of the major benefits of an information technology (IT) compatible automation solution like FactoryTalk Craft Brew. Data can provide a top-down view of operations, or drill down to specific items like ingredient traceability.
“And, on top of that, you can log recipes into the automation too. Even those who wake up at 4 am with the best idea for a new brew, can punch in the new recipe and it’s saved straight away, with all the info ready to be used in the future,” Bonacci said.
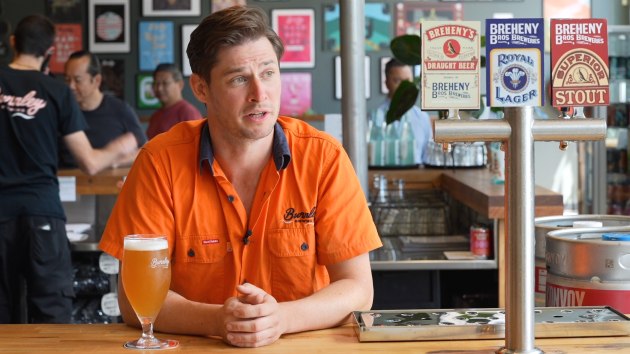
Stanzel believes Burnley Brewing is now in the perfect position to expand operations, and continue delivering unique, high-quality craft brews.
“With the automation solutions in place, we can now grow our brand, and we can take on more contract brewing agreements to keep supporting local, independent brewers. Bon Industry and Rockwell Automation have done a truly outstanding job with the new brewery, so all that’s left to say is cheers.”