It took two hungry brothers looking for ready-meal options post gym work-out to create My Muscle Chef. Last year the brand made $150 million in sales. Kim Berry talks to co-founder Tushar Menon. This article first appeared in the July 2021 issue of Food and Drink Business.
In 2013, Tushar Menon was finishing off his business degree and working in a sales call centre for an insurance company. His brother, Nish, was also working full-time.
“The small amount of spare time I had I’d spend in the gym, so I struggled to find time to prepare the kind of food I needed, which led me to look into ready-made options,” Menon tells Food & Drink Business.
“Nish and I both wanted quality nutrition after our workouts, but we quickly found that there wasn’t much variety in the market.”
What Menon did find were products almost solely focused on weight-loss and very few options with the protein content the brothers were looking for.
Side hustle bustle
The brothers rented a small commercial kitchen in Sydney’s Potts Point and started My Muscle Chef as a side hustle while they worked full-time.
“We hired two staff through Gumtree and brought in our dad to help out when we started delivering meals to people. With such a small team to start, it really was all hands on deck. I would even drive across the state to ensure customers were happy with their meals in the early days,” Menon says.
Throughout that first year, in 2013, they were making 1600 meals a week, growing the original customer base by sampling their meals at gyms around Sydney.
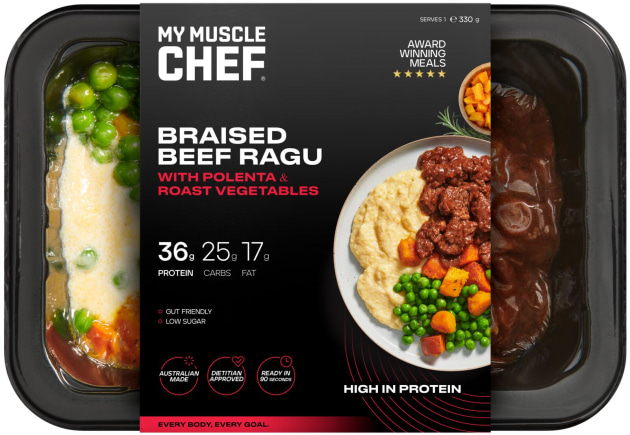
It became apparent very quickly that they had, indeed, identified a gap in the market. Just three months later, Menon quit his job at the call centre.
“After our first three months, we had about 300 customers spending $150 a week which is when I decided to quit my job.
“In its first year, My Muscle Chef brought in revenue of $827,000. By year two we were making around 3000 meals a week and brought in $1.5 million in revenue, and by year three we made 10,000 meals a week with $5 million in revenue.
“We’ve been fortunate to see consistent growth in the business, and last year achieved $150 million in sales,” he says.
All of that growth in the first three years came purely from word of mouth and sampling at gyms. It wasn’t until its fourth year that the company put money into advertising online.
“It seems so basic, but in those first years we focused on product quality. We wanted to make sure it would never be compromised.
“It also helped that we were the target market, so we could directly relate to what consumers were looking for.”
All meals are made in-house and it has been a non-negotiable for the pair since day one.
“When we started, the market perception of ready meals was that they were bland, boring, and lacking in flavour, so the quality of our meals was going to be pivotal to our success.
”We are both control freaks and we knew from the outset that having all production in-house was the only way to have full control over product quality,” he says.
Time to scale
In 2017, the business turned over $14 million with a financial outlook of $27 million for 2018.
The brothers realised they needed help if they were going to shift the business to the next level. They hired marketing, design, operations and quality assurance specialists; undertook market research based on the five years of data they had; and underwent a brand refresh.
But the biggest step they took was also what they saw, at the time, as a huge gamble – building their own factory.
Menon recalls, “Up until that point we had operated out of makeshift kitchens. We could have kept going at the pace we were at, but we made the conscious decision to grow.
“So, we reinvested everything we had earned in the last four years into constructing a state-of-the-art, custom built food manufacturing facility in Yennora, western Sydney.”
Point of difference
Menon is “incredibly proud” of the company’s manufacturing process, with its emphasis on chefs to maintain the home cooked feeling of its meals.
“Having chefs involved in the process means that, in comparison to other providers in the category that rely heavily on machinery, our meals are hand-made and cooked with love. It is something we’ve maintained from day one, our point of difference lies in the fact that each and every meal is prepared meticulously to ensure that taste, texture and restaurant-like quality,” he says.
The chefs work with the in-house dietitian and head of nutrition to develop meals catering to a range of health goals.
The company also pioneered vacuum seal technology in the ready-meal space in Australia.
“The technology was there, but it was only being used for raw meats and seafood.
“We saw it as an opportunity to lead the way and differentiate ourselves from competitors because it offered extended shelf life, improved product quality and maximised freshness.
“Initially, there was some feedback about how this new packaging caused the food to appear squashed, because our customers were familiar with our frozen products. However, we pushed ahead with the vacuum sealing due to its high calibre product retention, colouration and freshness over a longer period of time.
“Extended shelf life made for a seamless transition from frozen to fresh, and we’re proud to have introduced and championed this packaging innovation into the Australian ready-meals market,” Menon says.
Future goals
Menon says the company is well positioned for the projected growth in the ready-meals market. He says increasing penetration of pre-prepared meals is expected to grow from around $6.1 billion in 2020 to $9.1 billion in 2025. “Chilled foods represented roughly $2.3 billion and within that, around 30 per cent – $690 million – of revenue comes from direct-to-consumer sales.
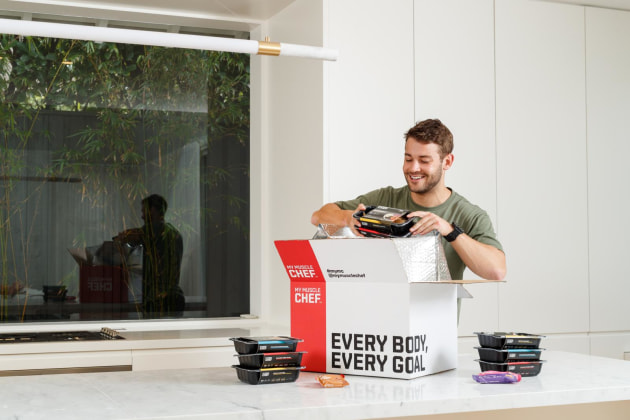
“There appears to be a slight shift away from frozen to chilled, with chilled foods – compared to frozen and meal kits – having the highest likelihood of people starting to purchase in the next twelve months. Between 29 to 35 per cent of people saying they might or definitely will purchase these items,” Menon says.
The company had a record year in 2020, with 400,000 unit sales and is launching nutritional snacks and beverages. From a side hustle to a multi-million-dollar enterprise, My Muscle Chef is lifting more than its weight.