Sludge dewatering is rarely seen in environmental or sustainability headlines, but it is an increasingly vital process in ensuring compliance with statutory groundwater, transport, disposal, and OHS regulations affecting both municipalities and industry. CST Wastewater Solutions managing director, Michael Bambridge, explains the best solutions for the food and beverage sector.
Sludge dewatering is the practice of minimising waste by volume to prepare the biosolids involved for effective disposal or re-use – and in so doing, avoiding sloppy hazardous spillages during expensive transport to equally expensive and increasingly rare disposal facilities.
It is a big undertaking, with sludge produced during virtually every wastewater treatment process that must be undertaken before the water can be released back into the environment.
Last year, the Australia and New Zealand Biosolids Partnership – a member-based group of utilities, consultants, academics and government bodies – estimated annual dry biosolids production rose to 372,000 tonnes.
With a weighted average solids content of dewatered biosolids around 23 per cent, this equates to 1.6 million tonnes of dewatered biosolids being carried around Australia. More than half the biosolids are transported between 50-400 kilometres for beneficial uses, such as the improvement of agricultural land and reclamations sites, including mine sites.
This ubiquitous sludge is a by-product extracted from the slurry during the many processes of municipal and industrial wastewater treatment of effluents, which can range ranging from human waste through to biological waste from industries such as food and beverage manufacturing including meat, fish and agribusiness.
Breweries are a good example of water-intensive industries that have rapidly become aware that their responsible use of water as a shared community resources is critical to their social licence to operate.
Statistics on this are many and varied and depend on whether you measure just what happens in the brewery itself, or measure the total footprint, including the farms where inputs are grown.
Some published accounts suggest giants such as AB InBev have reduced their water consumption to closer to 3-3.5 litres of water per litre of beer produced, compared with figures of perhaps twice that for larger industries and three or more times that for craft breweries.
I presume these figures relate to the breweries themselves, in which the two main uses for water are in the beer itself, and in the brewing process for activities like cleaning, cooling and pasteurising. And the breweries may correctly say they cannot control water practices in all agriculture.
But I was encouraged to note recent announcements by a brewing giant like AB InBrew, which advocates brewing sustainably and responsibly, now and for the future. AB InBrew produces well over half a million hectolitres of beer annually in recent years through its 175 major breweries and its spread over 50 countries. And what is outstanding is that water and wastewater is a top priority for leading brewers these days, a trend that will inevitably be followed by smaller and craft brewers, on which I offer some comment later.
And we should note that agriculture itself is a huge user of water, with the latest Federal DAFF report this year saying that Australian agriculture accounts for 55 per cent of Australian land use (426 million hectares, excluding timber production) and 74 per cent of water consumption (9981 gigalitres used by agriculture in 2021–22).
So, there is plenty of potential for sludge reprocessing and water recycling in agriculture, including in livestock processing and in crop processing – both areas in which efficient use of waste and water recycling are vital to our export future as environmentally responsible and sustainable water users.
Curtailing costs with sludge dewatering
Done well, dewatering can be an effective tool to reduce environmental hazards and to curb the expensive costs of transport of transport and disposal, as well as the carbon costs of transporting tens of thousands of tons of sludge over considerable distances.
Disposal costs can be a double whammy, with substantial specialised transport and carbon costs – before they even get to the front gate of the increasingly rare and scattered authorised disposal sites, which must be engineered to stop pollutants leaking into groundwaters, riverine and marine environments.
Done poorly, treatment and disposal of wet and sloppy waste can lead to hazards, both for the workers involved in removing and loading it, and instability of the ground and soil into which it may leak. There is also strong potential for groundwater contamination if the water removed is not properly treated.
SMEs benefit from low maintenance solutions
I’ve worked in wastewater treatment for more than 30 years, installing hundreds of water and wastewater treatment plants, filtration plants, anti-grit technologies from Smith and Loveless, as well as waste-to-energy plants for major food and beverage organisations.
We started manufacturing our own rotary drum screen and screw screen/compactors in Australia, to ensure we were doing as much as we could to ensure environmental protection. It was also to provide Australian companies with local quality assurance and backup service to ensure optimum performance even when supply lines are stretched, or in the event of environmental emergencies when statutory obligations and reputation are at.
When it comes to food and beverage manufacturers, we have seen the development of a strong need for better sludge treatment for small-to-medium public and private organisations.
Water and wastewater treatment and water recycling is not a one-size-fits-all. Each part of the food and beverage industry faces its own challenges, including responses to treatment of pollutants such as Biochemical Oxygen Demand and Chemical Oxygen Demand (BOD and COD) discharges of which can deprive waterways of the oxygen they need to avoid algal bloom, mass fish deaths and degradation of waterways.
Other pollutants that vary from industry to industry include Total Suspended Solids (TSS) as well as nutrients including nitrogen and phosphorous and pathogens and antibiotic-resistant bacteria.
Technologies we employ to address these issues include Dissolved Air Flotation (DAF) and rugged, locally manufactured rotary drum screens and fine inlet screening to optimise the performance of water treatment processes downstream from the primary screening process– including the increasingly prevalent Membrane Bioreactors MBRs process.
Membrane bioreactors (MBRs) are increasingly being used for water, wastewater treatment, and recycling throughout Australia and New Zealand, responding to climate change, shortages of land, operational cost-effectiveness, and technology advances for water recycling. These factors, plus cost of operation and maintenance, are also driving the need to include fine screening of both MBRs, and conventional activated sludge treatments, to protect downstream equipment and processes, preventing blockages and equipment breakdowns, which end up breaching discharge conditions and pollution entering the environment.
MBR technology has advantages over conventional methods in the food and beverage industry, including the fact that there are no chemical reagents or additives utilised, and the product is clean. When done in a closed system, such as an enclosed tank membrane bioreaction, the separated food doesn't experience browning or colour degradation.
Some applications require even more specific technologies or combinations of technologies, such as Moving Bed Biofilm Reactors, MBBR), Reverse Osmosis (RO) and Sequencing Batch Reactors.
So, you can appreciate, water treatment isn’t for bargain hunters. You must engineer quality inputs to get quality outputs. Buying a cheap import that might not even be suitable for your company’s output will end up costing the business more – in servicing, breakdowns, statutory fines, and reputational damage.
Specifically for our SME customers, we work with companies using some of the most advanced technologies in the Asia-Pacific. For example, the Japanese-made stainless steel KDS low-maintenance liquid-to-solid waste separator, which reflects the attention to detail and quality ethos of its country of origin.
The KDS separator is right for environmentally aware small-to-medium operations because unlike a belt press or a screw press, it uses a fraction of the power of a centrifuge and consumes no water during operation.
For an SME it is a relatively low investment cost because it offers a high-performance alternative to sludge drying beds and geobags.
KDS separator benefits
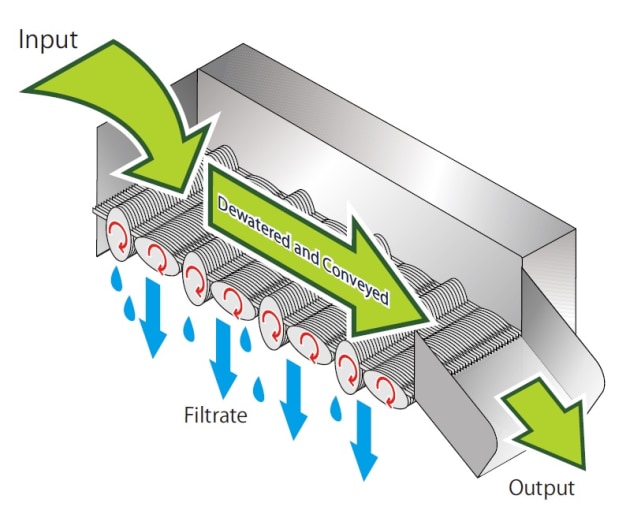
which is available in hydraulic capacities from 264-4092 gal/hr (approximately 1000-15490 litres)
with input solids content of two per cent. (Image: CST Wastewater Solutions)
The industry has faced – and is facing – significant challenges. We hear the difficulties our customers are experiencing – interest rates, cost-of-living impacts, energy prices, and supply issues. Our focus is to provide solutions to operational issues that can reduce costs and improve the environmental performance of the company.
Used for thickening of dissolved air flotation sludge – a very common application throughout wastewater operations – the KDS achieves solids capture of 97 per cent thickened sludge at a dryness of 17 per cent. Waste activated sludge dryness levels are typically 15-25 per cent.
KDS technology removes more than 50 per cent of the water from wastewater sludge to provide a 50 per cent reduction in transportation costs. It features a unique self-cleaning dewatering and conveying system with oval plate separation and transfer structure that prevents clogging and permits automatic continuous operation that handles oily and fibrous material with ease
Small-to-medium applications for which the separator is designed include:
- intensive livestock and aquaculture operations, including abattoir, feedlots, fisheries, poultry and dairy farm wastewater and sludge. Cattle manure cake dryness of 25-35 per cent is typically achieved;
- food and beverage processing waste, including snack foods, kitchen and restaurant waste, brewery waste, raw wastewater (primary screening) and sludge;
- pig farm raw manure and sludge, with cake dryness of 20-30 per cent; and
- barrel polishing water, water-based paint wastewater, grease trap waste, dyeing wastewater, waste oil, and plastic recycling.
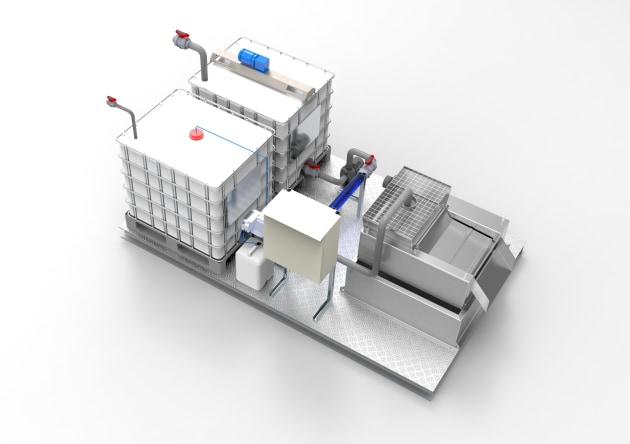
(Image: CST Wastewater Solutions)
The new skid-mounted KDS technology offers potential users a highly effective plug-and-play solution to waste processing needs. Measuring only 3.8 by two metres, it offers the type of low-maintenance high efficiency that is so important where agribusiness, industrial and municipal operations don’t have the resources to place engineering staff on close standby.
Tailored solutions
As environmentally aware and quality-focussed wastewater treatment professionals, we don’t ever propose that just one solution is the answer to all water quality issues – that would be absurd. There are many excellent technologies out there, of which KDS is an example in the small-to-medium separator category.
For example, at the large end of the scale, he has installed a large-scale Global Water and Energy (GW&E) COHRAL waste-to-energy anaerobic digestion system for the Oakey export meat works of NH Foods.
GW&E COHRAL systems are part of a broader range of anaerobic digestion technologies which in recent years have seen a strong development of anaerobic digestion units worldwide, especially in the US, EU, and China.
Anaerobic digestion uses microorganisms that thrive in oxygen-free environments to digest waste (feedstock) inside tanks. One byproduct of the process is methane, which rises to the top of the tank and is collected. The gas can be used as-is to fuel boilers or it can be refined further and sold in established markets. The leftover solids (digestate) are also marketable in agriculture. Anaerobic digestion is a process where microorganisms degrade organic matter in the absence of oxygen to produce biogas, mainly composed of methane and carbon dioxide.
The bacteria contained in a compact, closed and clean anaerobic plant consume typically 90-99 per cent of organic contamination (COD) in the waste stream, so that the water goes back to the environment often cleaner than the sources from which it was drawn.
The beauty of anaerobic systems is that they work on any biological waste stream, be it a food, beverage, dairy, meat, livestock or crop agribusiness or a municipal waste-to-energy plant.
CST Wastewater Solutions has installed anaerobic systems for meat, fruit and brewery operations in Australasia. GW&E technology involved is one of the best proven internationally.
The dairy industries in Australasia are among a number of primary production and agricultural industries that are good candidates for anaerobic digestion. Dairy plants have to deal with organic byproducts like whey, buttermilk, and wastewater from cheese processing. It can be difficult and costly to treat the effluent for compliance with discharge regulations. And, if a local wastewater utility treats the discharge, it may charge extra for the high organic load.
So good technologies are there and available for use across the food and beverage production and processing chain.
Our main message to environmentally responsible organisations is to engineer for future quality of water output and reliability. Don’t just join the race to the bottom, on upfront pricing alone. Typically, what that does is transfer problems down the line, where the costs can be far greater. There is always a reason why things are cheap. Our water resources deserve better.