Nestlé Professional’s multi-million dollar investment in its Smithtown, NSW factory will bolster local manufacturing and support collaborative product developments – starting with a new recyclable cup for Hot Chockee, developed in partnership with Wellman Packaging and 7-Eleven.
The Smithtown facility, where popular products like Milo, Nesquik and Nestlé hot chocolate are also made and packaged, will now have capacity to produce 4.7 million cups of Hot Chockee over the next twelve months. Hot Chockee, a ready-to-go cup filled with hot chocolate powder, was previously imported from Europe, making the project a big win for manufacturing in Australia and specifically for Smithtown in regional NSW.
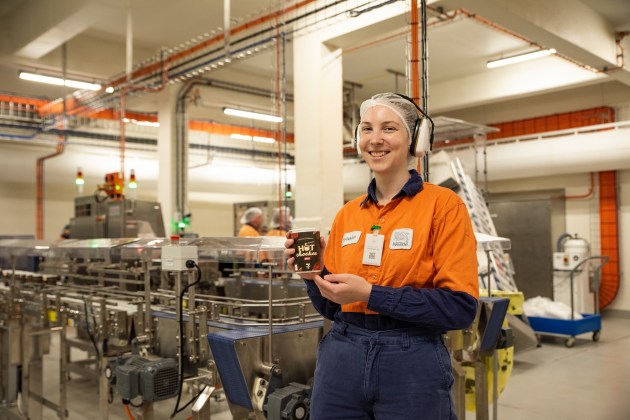
Nestlé Professional Oceania general manager Kristina Czepl said, “The recent investment into the Smithtown factory has allowed us to collaborate on exciting new packaging solutions. It is a great example of working with likeminded partners to pioneer alternative materials to facilitate better recycling.”
The new polypropylene (PP) Hot Chockee cup, including the PP label and foil seal, is accepted through kerbside recycling as verified by the PREP tool, and carries the Australasian Recycling Label with clear disposal instructions. This move could save up to 95 tonnes of waste from entering landfill each year, according to Nestlé Professional.
7-Eleven head of Sustainability, Fiona Baxter said, “We are incredibly proud to continue our partnership with Nestlé Professional and invest in innovative packaging solutions. Our new 7- Eleven Hot Chockee still has the same delicious taste, made and packed in Australia, with approximately 68 per cent of ingredients sourced locally. This innovation helps both Nestlé and 7-Eleven to continue to work together towards our packaging sustainability targets.”
The project unpacked
PKN spoke to Stephanie Rajczyk, Nestlé Manufacturing Services manager, Product Technology and Development, about the technology installed to support the cup production.
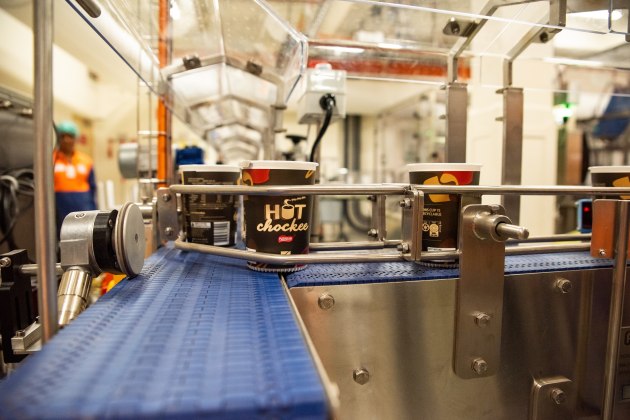
Rajcyk said two major lines have been installed at the Smithtown factory. One is a cup filling line which fills each cup with the right amount of product, and then seals the foil to the ledge inside the cup. The other is a flow wrapping machine which collates and wraps the cups into sleeves of eight, ready for packing into cases.
“The project has been in the works for over three years, but the development was delivered in 18 months. We’ve worked in partnership with Wellman Packaging to develop the cup right here in Australia,” Rajcyk said.
Speaking to PKN, CEO of Wellman Packaging Craig Wellman explained that the new cup represents a significant advancement over the previous cup, which was a poly coated, multi-wall, paper cup that was then inserted with an injection moulded polyethylene tub to carry the powder, which together prevented recycling of the cup.
What Wellman Packaging has achieved is a mono-material PP solution, removing the recycling impediment.
“From a technical performance perspective, we have substantially improved the insulation characteristics by virtue of the external ribs, which are then wrapped by the PP label,” Wellman said.
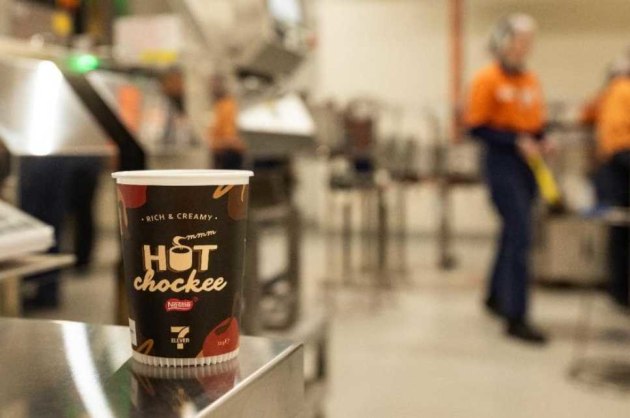
“While the new cups are lighter overall than the previous composite paper cups, they are sturdy enough and dishwasher safe to be reused multiple times at home, perhaps for hot beverages or collected for children’s parties,” Wellman added.
“The design of the cups, trademarked as Thermocup, using Wellman’s globally patented IsoTherm technology, represents a major step forward compared to similar products on the market – given the depth and coverage of the iso-ribs which are extremely thin so as to minimise the part weight – something that a number of the most respected toolmakers in the world told us couldn’t be done,” he said.
The moulds were designed and built in Australia, with Wellman’s in-house design and engineering team developing the technology from concept.
Product trials
Explaining what was involved in the product trial phase, Rajcyk said, “Once the plastic moulding tooling was developed, trial cups were then sent to the equipment supplier overseas, along with the foil seals, so that we could conduct our factory acceptance testing on the cup filling production line, before the equipment was shipped to Australia.
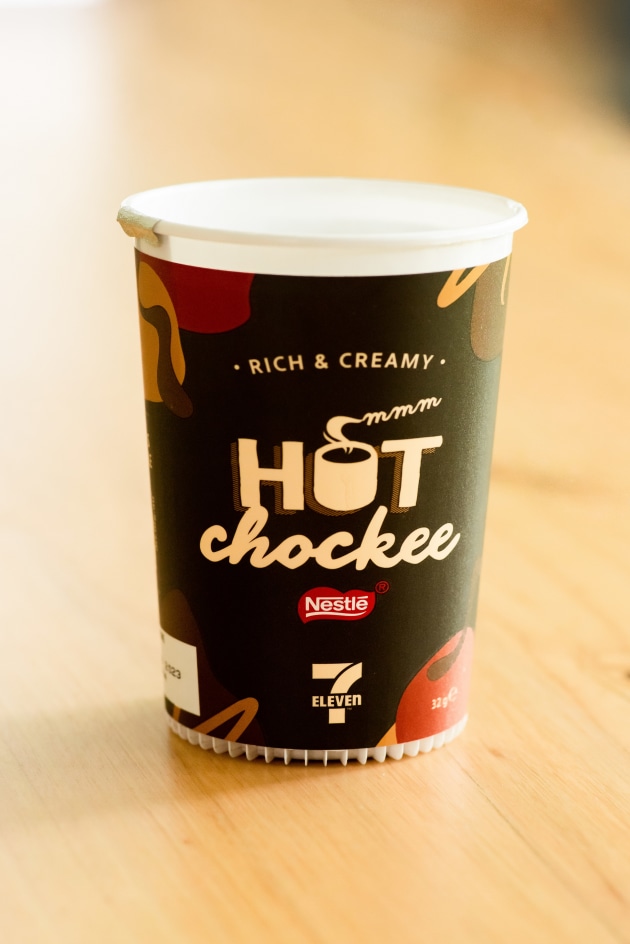
“Then the cups filled with chocolate powder were sent to our flow wrapping equipment manufacturer to trial that part of the line.
“Once all parts of the production line arrived in Australia, they were assembled to test production in sequence and synced with our bulk powder delivery system, labelling machine, check weighers, coders, X-ray machines,” Rajcyk said.
Wellman said the project was delivered with a “holistic, end-to-end approach”. This included not only the cup design itself but all associated injection moulds and special purpose equipment which has been integrated with an all-electric injection moulding machine from German machinery supplier, Arburg.
Working very closely with Nestlé and its partners, including machinery supplier JL Lennard, Wellman Packaging has also designed, and will construct, the materials handling solution for the cups using returnable and reusable packaging, to provide a closed loop, turnkey solution and representing a further reduction in the carbon footprint of the project.
Taking this to the next important step, Wellman Packaging is developing a closed-loop, food-grade recycling program for the cups, which it hopes in time, will allow the collection, recovery and reprocessing of cups back into new cups.
Wellman says its trademarked Isotherm technology holds broad application, including to other thin-wall packaging such as coffee cups and noodle tubs, and the company is already exploring opportunities in these areas.
Wellman Packaging is also in discussions with its trading partners in Europe and the US for the use of the technology in their markets.
“We are extremely excited about the potential of the technology,” Wellman said, “and extremely proud to have partnered with Nestlé Professional to bring this project to fruition.”
Nestlé is ranked #12 in Australia’s Top 100 Food & Drink Companies 2022 report.