Treasury Wine Estates says the integrated automation and barrel handling system at its Barossa Valley winery in South Australia is a world first. It is the latest investment at the site, which cost $165 million, and was officially opened in 2022.
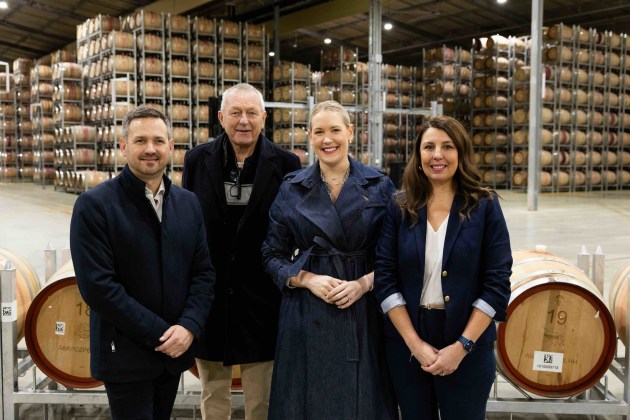
The end-to-end automation features nine autonomous guided vehicles (AGVs), a custom barrel management software system, automated barrel washing and filling facilities, and individual barrel identification.
It was almost four years in the making, project planning and trials started in late 2020, with the integrated system commissioned and fully operational in June 2024.
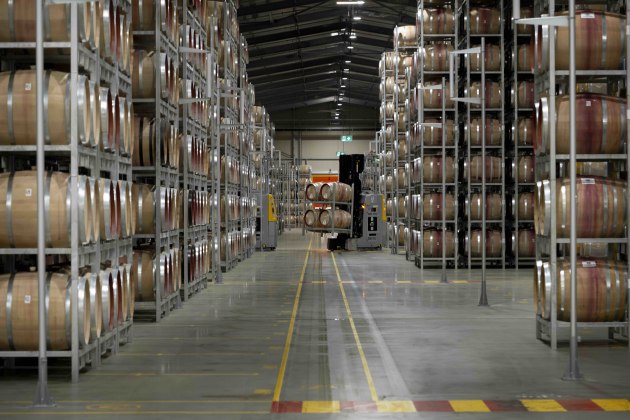
(Source: Treasury Wine Estates)
The AGVs are controlled by a customised digital barrel management system that TWE developed with digital technology company, Nukon, part of the SAGE Group. The laser-guided AGVs in the 35,000m2 barrel hall were tailored to the site by Italy-based automation provider E80 Group.
The set-up means the TWE’s winemaking team can control the system remotely to move barrels through the maturation process.
The company said, “Integrating these components in an end-to-end automated system makes this a world-first in winemaking, bolstering the Barossa Valley’s credentials as one of Australia’s most innovative winemaking regions.”
The process currently runs 24 hours a day, five days a week, and is expected to boost the red wine handling capacity of the hall to 125,000 barrels.
This latest investment expands the site’s production capacity by up to 60 per cent and enhances traceability of the barrels across their life cycle. It also reduces energy consumption and creates a safer working environment by minimising manual handling tasks.
TWE chief Supply & Sustainability officer, Kerrin Petty, said, “Our Barossa Valley site is fast becoming an international hub of innovation in winemaking, sustainability and resilience.
“Introducing full automation in our barrel hall increases our luxury and premium winemaking capacity, so we can craft more of our renowned wines for wine lovers around the world while creating a safer working environment for our people.”
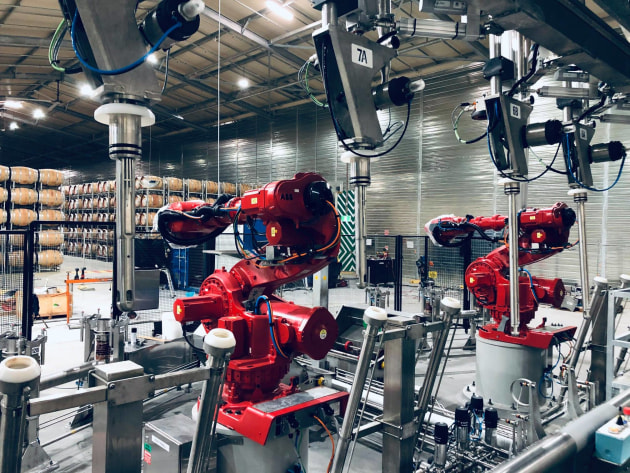
(Source: Treasury Wine Estates)
Petty said the automation optimises how team members are allocated in the barrel hall. The site’s former forklift operators have either been re-skilled to operate the digital barrel management system and manage the new automated vehicles or moved on to other roles at the site.
The enhanced data and analytics in the automated end-to-end system create greater traceability and improved quality for the site’s 60,000 barrels of wine across brands including Penfolds, Pepperjack, and Saltram, the company said.
The lithium battery powered vehicles, powered by 100 per cent renewable electricity also contribute to TWE’s goal of achieving net zero emissions by 2030.
TWE director of Supply Technology, Jodie Rowlands, said, “We’ve seen improvements in safety, efficiency, and traceability in our barrel hall, with the team on site embracing the new way of working. The efficiency and precision of automated, sensor-based forklifts to transport the barrels lowers energy consumption compared to manual handling processes.”
The state-of-the-art Barossa Valley facility opened in 2022 after a $165 million extension that expanded the production and storage facilities by a third, making it the winemaker’s largest bottling operation globally.
Since then, more than 6000 solar panels have been installed and produce up to a quarter of its electricity needs, together with a wastewater treatment plant and stormwater capture that feeds a nearby 254-megalitre lined dam.